
How can millions of samples be analyzed faster? Sebastian Steiner (left) and Patrick Henke find technical solutions to such questions.
Own creations
Technology for the lab
Sebastian Steiner leads a team of in-house engineers that designs and builds technical solutions for R&D and breeding. For example, they develop everything from large DNA extraction machines to small devices that make everyday work easier.
Some might remember the early years of marker analysis at KWS: In the 1990s, single-channel pipettes were enough to handle a handful of samples. However, more automation became necessary as the processes evolved. Single-channel pipettes became 8-channel pipettes, and, gradually, pipetting robots. The growing degree of automation significantly improved the speed of laboratory processes.
At KWS, lab automation is particularly crucial at Marker Service, who offer centralized analyses for all our crops. “We are talking about several million incoming samples every year, a figure that has more than doubled every five years recently,” states Cornelia Glass, Group Lead at Marker Service.
Molecular markers
Genotyping is the process of determining an individual’s genetic make-up. Marker-assisted selection is used to select desired traits directly from genetic material, making breeding more efficient.
Genetic or molecular markers are DNA segments that are associated with specific traits and that have a known location within the plant’s genome. These markers can be rapidly analyzed from the DNA of small leaf or seed samples. If the analysis confirms that the plant carries the marker for the desired trait, it is selected.
In genomic selection, the DNA of the plant can be analyzed for thousands of such known markers. With the help of computer modelling, combinations of best suitable traits can be calculated to determine the breeding value of young plants.
Apart from selection of plants based on their genotype, marker services are used in quality control and seed purity testing, for example.
The first step in marker analysis is DNA extraction, a process where the plant’s DNA is separated from cellular components and purified for further analyses. Extraction typically forms the analysis bottleneck; its capacity determines the delivery of all further analyses. To solve these types of problems, High Throughput Services hosts a Technical System Engineering team, led by Sebastian Steiner, molecular biologist by background.
“With the high demand of throughput and cost reduction required in genotyping processes, we are thinking beyond single process automation. Solutions available in the market are very costly, and designed toward human diagnostics or research purposes,” explains Sebastian Steiner. “We are moving on to an industrial approach of lab automation – with production lines and 24/7 operation of a molecular biology lab.”

The advantage of having your own team: Technical solutions can be implemented as desired and cost less than from external providers, says Joachim Strauß.
Advantages of in-house engineers
For example, the team implemented various facilities for automated DNA extraction, image processing and sample logistics and is currently working on new facilities that will contribute to further increases in efficiency. “And if we can further improve our workflows, that means decreasing the price of individual analyses for our internal customers, which are the R&D groups and breeders,” he continues.
Having an in-house group of engineers for lab automation and process improvement gives KWS the kind of flexibility that is needed to serve the varying needs of the different groups and breeding stations. “Increasing efficiency is our main challenge,” confirms Cornelia Glass.
“THE CLOSENESS TO OUR CUSTOMERS IS REALLY HELPFUL."
Patrick Henke
Less dependent on external service providers
“But we also need the team to develop our own customized solutions,” adds Markus Niessen, Senior Group Lead at Marker Service. Worth mentioning here is the development and production of own laboratory consumables. “Especially after the experiences during the coronavirus lockdowns and the resulting interrupted supply chains, we want to be less dependent on external suppliers and are glad to have built up our own capacities here and to produce our consumables locally ourselves.”
“Our group is independent, but at the same time, well connected,” summarizes Patrick Henke, the electrical engineer in the group who has his focus on machine design and software development. The team works closely with internal customers: Marker Service, Cell Service, Molecular Breeding teams and many other groups. Projects are always initiated with the definition of an opportunity for improvement, after which the team explores existing solutions or partners in the market; sometimes, a good customizable option is found this way. If not, the specifications are drafted, and the design process starts. “It really helps to be so close to our internal customers,” states Patrick Henke. “We already know their needs quite well, and we can meet up with them regularly during the process, making sure that we are seeing things the same way. At the end, we support them in taking the new device into use.”
“Working like this, we can deliver exactly what is needed,” says Joachim Strauß, mechanical engineer of the Technical System Engineering group. “We used to need to contact suppliers for very specific requests that were sometimes hard to realize – having our own team gives us the flexibility to get things done, as well as saving a lot of money.”
Beyond automation
But there are big differences in requirements between the different customers. Sebastian Steiner takes an example of the “KWS scissors”– special, customized type of scissors developed for the Cell Service that can cut, hold, and place plant samples in a sterile environment without dropping them as normal scissors would. In addition, the team developed manual tools for the sampling of leaves and seeds.
“Working with plants and living material, there will always be processes that simply cannot be automated,” says Joachim Strauß. “But where problems are identified, we can help develop a solution.”
Views
"New creative solutions are needed"

Joachim Strauß, mechanical engineer
“I have been with KWS for nine years and have experienced the fast development of lab automation first-hand. From sampling to laboratory analysis, we have improved many process steps and helped shape the processes. I can still remember one of my first inventions for KWS sugarbeet – the SeSam (Seedling Sampling) system is still used to take high-throughput samples from seedlings. As an engineer, what particularly appeals to me about my work is the interdisciplinary work in biological issues. I can help with topics with my differentiated perspective and at the same time learn more about the biological aspects of the individual processes. In this job, no two days are the same.”
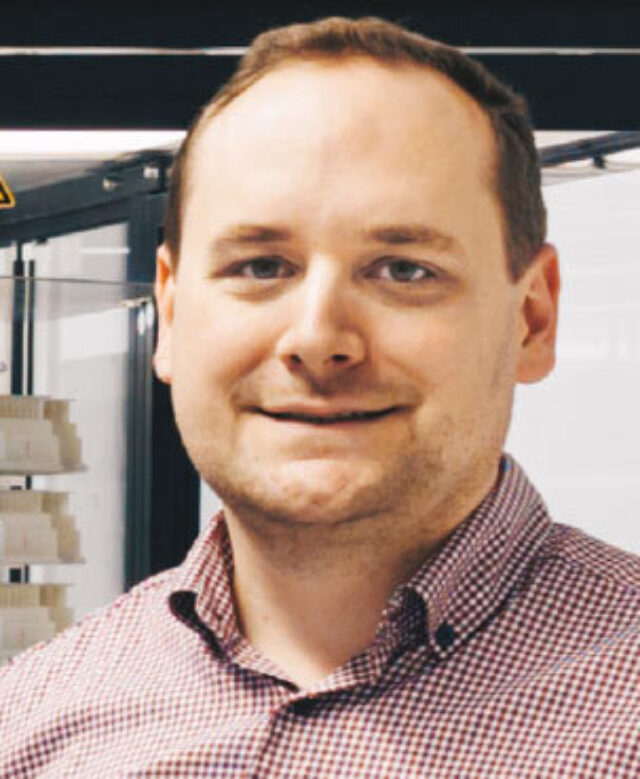
Patrick Henke, electrical engineer
“I’m happy with my nearly four years at KWS, although for an engineer with no agricultural background, a plant breeding company was not an obvious career choice. I find it very exciting to be part of the transformation of lab automation for the agricultural sector. Unlike other industries, there are few well-trodden paths here, but new creative solutions are in demand and must be found by us. I see it as an endless green field of opportunities.”
This article is from insideKWS, the employee magazine of KWS. If you are an employee of our company, you have access to all other articles and previous issues.
© KWS SAAT SE & Co. KGaA 2025